

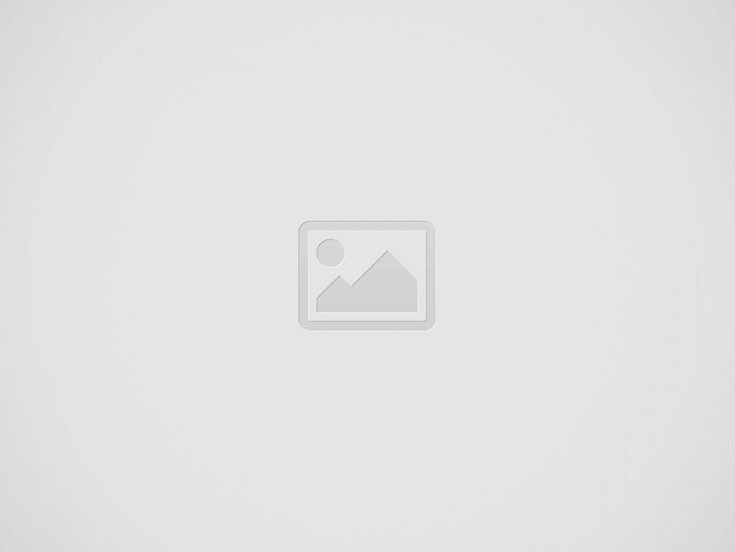
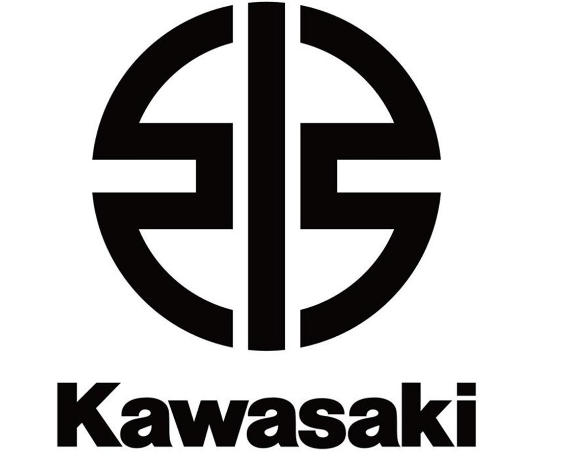
2022 Kawasaki KX112 Front Suspension


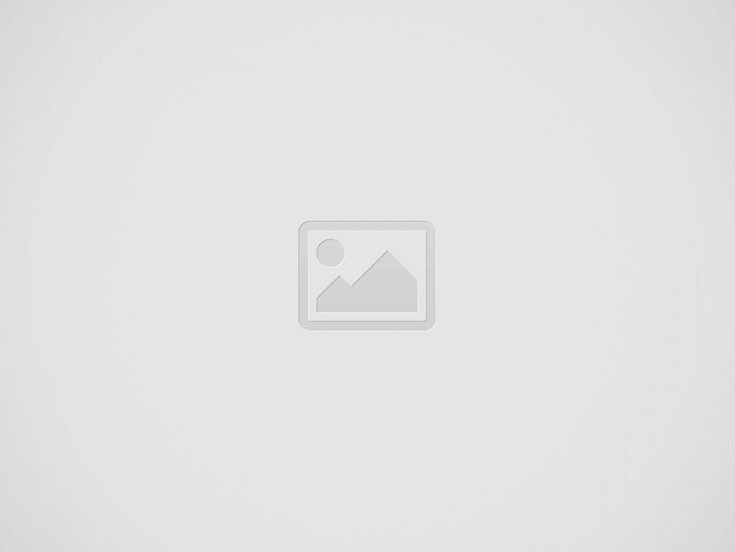
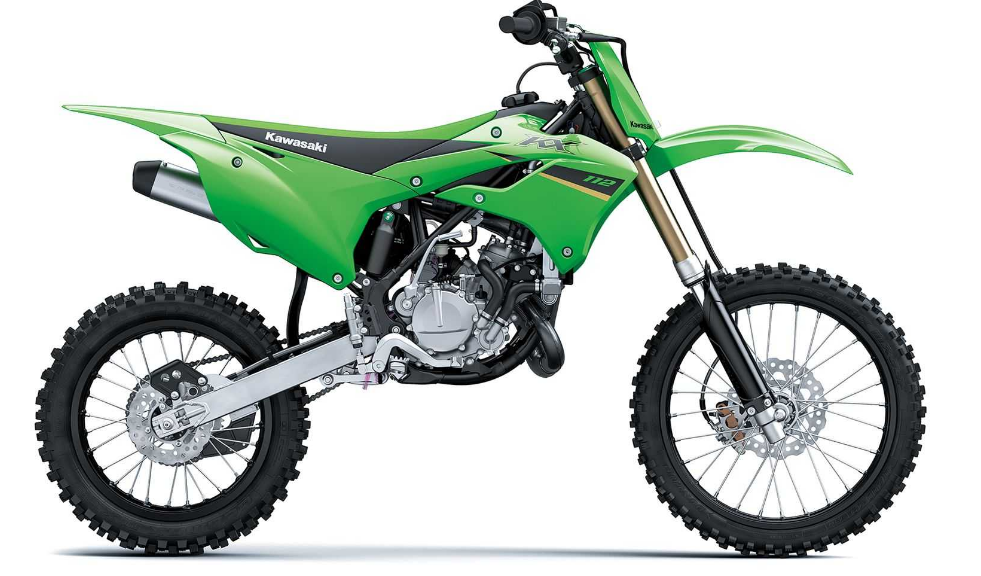
Front Suspension
Front Fork Inspection
NOTICE
- Sticking muds or dusts on the sliding surface of the front fork could damage the oil seal,leading to an oil leak. Clean the sliding sur face after each ride.
- Holding the brake lever, pump the front fork back and forth manually to check for smooth operation.
- Visually inspect the front fork for oil leakage, scoring or scratches on the outer surface of the inner tube.
- If necessary, replace by an authorized Kawasaki dealer.


- A. Inner Tubes
NOTICE
If the inner tube is badly bent or creased, replace it. Excessive bending, followed by subsequent straitening, can weaken the inner tube.
Front Fork Adjustment
- Any of the following front fork adjustments should be made to tune the front suspension to the rider’s weight and the condition of the track.
- Basically, there are five adjustments you can make to the front fork.
- Air Pressure Adjustment
- Air pressure acts as a progressive spring over the entire fork travel range. Since the air pressure in the fork legs increases with normal use, the fork action on your KX will get stiffer as the race progresses.
- Therefore, it is not recommended to increase the air pressure for additional springing. The KX forks are designed to function without added air.
- Compression Damping Adjustment
- This adjustment affects how quickly the fork compresses. The fork compression damping adjuster has at least 20 positions. The fully seated position (adjuster turned fully clockwise) is the hardest setting. Turning it counterclockwise 20 clicks from the fully seated position is the softest setting.
- Fork Oil Level Adjustment
- The fork oil level affects only the final 100 mm (4 in.) of fork travel. A higher oil level will make the fork rebound more quickly. A lower oil level will make the fork rebound more slowly.
- Optional Fork Springs
- Optional springs, softer and stiffer than standard, are available.
- Fork Height
- Steering is greatly affected by the fork height (how much the outer fork tubes protrude above the up- per fork clamp). The less the fork tube protrudes, the lighter the front end becomes and the greater the tendency for understeering and washout due to weight bias. Increasing the amount of fork tube protrusion has opposite effects. Be sure that the front tire does not touch the fender when the fork is fully compressed. Make this adjustment in 10 mm (0.39 in.) steps.
NOTICE
The right and left fork tubes must be adjusted evenly.
Air Pressure Adjustment
- The standard air pressure in the front fork legs is atmospheric (0 kPa, 0 kgf/cm2, 0 psi). Air pressure in the fork legs increase with normal use, so the fork action stiffens during operation. Release air pres- sure from the fork legs prior to each race through the air pressure relief screw located in front fork top plug. Make sure the front forks are fully extended with the front wheel off the ground when releasing the pressure.
- Raise the front wheel off the ground using a jack (special tool: 57001-1238) and attachment (special tool: 57001-1608).
- Remove the air pressure relief screw on each front fork top plug to let the air pressure equalize. Then, tighten the screws to the specified torque.
Tightening Torque
- Air Pressure Relief Screws: 1.3 Nm (0.13 kgfm, 12 in lb)


- A. Air Pressure Relief Screw
- B. Front Fork Top Plug
Compression Damping Adjustment
- Raise the front wheel off the ground using a jack (special tool: 57001-1238) and attachment (special tool: 57001-1608).
- Clean the bottom of the fork tubes.
- Remove the caps on the bottom of the fork tubes.

- To adjust the compression damping, turn the adjuster on the compression valve assembly with a flat tip screwdriver. Adjust the compression damping to suit your preference under certain conditions.
NOTICE
Do not force the compression damping adjuster beyond the fully seated position, or the adjusting mechanism may be damaged.

- A. Compression Damping Adjuster
- B. Compression Valve Assembly
Compression Damper Settings


- A. Seated Position (Adjuster Turned Fully Clockwise)
- B. Softer (Counterclockwise)
- C. Harder (Clockwise)
- D. Standard Setting
A number of turns counterclockwise usable range 20 clicks or more.
Standard Compression Damper Setting
Counterclockwise from the fully seated position
NOTICE
The right and left fork tubes must be adjusted evenly.
- Install the caps on the bottom of the fork tubes.
Front Fork Oil Change
Thoroughly clean the forks before disassembly.
NOTICE
- Be careful not to scratch the inner tube and not to damage the dust seal.
- Avoid scratching or damaging the inner tube or the dust seal. Use a mild detergent and sponge out dirt with plenty of water.
NOTE
- Record the compression damper setting before disassembling.
- Set the compression damping to the softest settings before disassembly to prevent the needle of adjusters from damping.
- Remove the brake caliper from the fork leg, and rest the caliper on some kind of stand so that it does not dangle.
- Insert a wood wedge between the disc brake pads.
- This prevents them from being moved out of their proper position if the brake lever is squeezed accidentally.
- Remove the brake hose clamps and both fork protectors.
- Remove the cotter pin and front axle nut.

- A. Brake Caliper Mounting Bolts
- B. Brake Caliper
- C. Brake Hose Clamp Bolts
- D. Brake Hose Clamps
- E. Fork Protector Bolts
- F. Fork Protector
- G. Cotter Pin
- H.Front Axle Nut
- Raise the front wheel off the ground using a jack (special tool: 57001-1238) and attachment (special tool: 57001-1608).
- Remove the axle, and pull out the wheel. Take off the collar from each side of the front hub.
NOTICE
Do not lay the wheel on the ground with the disc facing down. This can damage or warp the disc. Place blocks under the wheel so the disc does not touch the ground.

- Remove the number plate (see Steering section).
- Loosen the front fork clamp bolts (upper).
- Loosen the front fork top plug.
NOTE
- Do not remove the front fork top plug.
- Loosen the front fork clamp bolts (lower).


- A. Front Fork Clamp Bolt (Upper)
- B. Front Fork Top Plug
- C. Front Fork Clamp Bolts (Lower)
Remove the front fork by pulling it down while twisting it.

- A. Pull down by twisting.
- B. Front Fork
Remove the top plug from the outer tube and slowly slide it down the outer tube.

- A. Top Plug
- B. Outer Tube
- C. Slide Down
- Compress the fork spring and install the fork spring holder (special tool: 57001-1286) between the push rod nut and spring seat.
- While holding the front fork push rod nut with a wrench, remove the front fork top plug from the top of the push rod.
- Remove the fork spring seat and fork spring.


- A. Front Fork Spring Holder (Special Tool: 57001-1286)
- B. Wrench
- C. Front Fork Top Plug
- D. Front Fork Push Rod Nut
- E. Fork Spring Seat
- F. Fork Spring
Place a drain pan under the front fork and drain fork oil.
NOTE
Pump the push rod several times to drain the fork oil.

- Hold the front fork at the inverted position for more than 20 minutes to allow the fork oil to fully drain.


- Clean the threads of the front fork top plug and outer tube.
- With the piston rod fully stretched, pour 310 mL (10.5 US oz.) of fork oil.
NOTE
While filing the fork oil, take care to keep the oil level topped off that it stays above the two lager holes near the top of the inner tube.

- A. Fork Oil
- B. Cylinder Unit
Suspension Oil
- A15-10 (1 L): P/No. 44091-0004
Standard Fork Oil Amount (Cylinder Unit)
- Install the push rod puller (special tool: 57001 -1298) onto the push rod.
- Fill the fork cylinder with oil by gently moving the push rod puller up and down five times.
- Fill oil between the inner tube and outer tube by pumping the outer tube up and down five times.
- Adjust the fork oil level within the adjustable range to suit your preferences.
Standard Fork Oil Level
- 95 +2 mm (3.74 +0.08 in.)
Adjustable Range
- 75 115 mm (2.95 4.53 in.)
Remove the excess oil through the outer tube opening, using an oil level gauge (special tool: 57001-1290).

- A. Oil Level Gauge (Special Tool: 57001-1290)
- Pull up the push rod puller.
- Install the fork spring and the fork spring seat.
- Replace the top plug O-ring with a new one.
- Check the front fork push rod nut on the bottom of the thread.
- Compress the fork spring and install the fork spring holder (special tool: 57001-1286) between the push rod nut and spring seat.

- A. Push Rod Puller (Special Tool: 57001-1298)
- B. Fork Spring Holder (Special Tool: 57001-1286)
- C. Fork Fork Push Rod Nut
- D. Fork Spring Seat
- E. Fork Spring
- F. O-ring
- Remove the push rod puller and screw the front fork top plug onto the push rod.
- While holding the front fork push the rod nut with a wrench, and tighten it to the specified torque.

A. Front Fork Push Rod Nut - B. Front Fork Top Plug
- C. Push Rod
- D. Wrench
- Tightening Torque
- Front Fork Push Rod Nuts:
- L 15 Nm (1.5 kgfm, 11 ftlb)
- Temporarily tighten the front fork top plug fully Confirm the stroke of the front fork.
- Install the front forks to the motorcycle.
- Adjust the fork height (see Fork Height Adjustment section).
- Tighten the front fork clamp bolts (lower) to the specified torque.
- Tightening Torque
- Front Fork Clamp Bolts (Lower):
- 20 Nm (2.0 kgfm, 15 ftlb)
NOTE
- Tighten the two clamp bolts alternately two times to ensure even tightening torque.
- Tighten the front fork top plug to the specified torque.
- Tightening Torque
- Front Fork Top Plugs: L 28 Nm (2.9 kgfm, 21 ft:lb)
- Tighten the front fork clamp bolts (upper) to the specified torque.
- Tightening Torque
- Front Fork Clamp Bolts (Upper): 20 N-m (2.0 kgf m, 15 ftlb)
- Apply high-temperature grease to the oil seals of the wheel.
- Install the collars on the left and right sides of the hub.
- Put the front wheel assembly between the fork legs.
- Apply a thin coat of grease to the front axle for rust prevention.


- A. Front Axle
- B. Grease
- C. About 70 mm (2.8 in.)
- D. About 10 mm (0.4 in.)
NOTE
- Do not apply grease to the threads of the axle.
- Insert the front axle from the right side of the motorcycle.
- Tighten the front axle nut to the specified torque.
- Tightening Torque
- Front Axle Nut: 80 Nm (8.2 kgfm, 59 ft-1b)
- Replace the cotter pin with a new one.
- Install a new cotter pin through the front axle, and bend its ends.


- A. Cotter Pin
WARNING
- A loose axle nut can lead to an accident resulting in serious injury or death. Tighten the axle nut to the proper torque and install a new cotter pin.
- Remove the jack and attachment.
- Take out wood wedge between the brake pads.
- Install the brake caliper to the fork leg, and tighten the brake caliper bolts to the specified torque.
- Tightening Torque
- Front Caliper Mounting Bolts: 25 N-m (2.5 kgf m, 18 ft:lb)
- Install the fork protectors so that they do not touch the front fork outer tube, and tighten the bolts to specified torque.
- Tightening Torque
- Fork Protector Bolts: 3.5 Nm (0.36 kgfm, 31 in-lb)
- Install the brake hose clamp, and tighten the bolts to specified torque.
- Tightening Torque
- Brake Hose Clamp Bolts: 7.0 N-m (0.71 kgf m, 62 in-lb)
- Check the front brake for good braking power and no brake drag.
WARNING
After service, it takes several applications of the brake lever before the brake pads contact the disc, which could result in increased stopping distance and cause an accident resulting in injury or death. Do not attempt to ride the motorcycle until a firm brake lever is obtained by pumping the lever until the pads are against the disc.
- Check the clutch lever and throttle for the proper operations.
- Adjust the compression damping force adjuster
Optional Fork Springs
- Various fork springs are available to achieve suitable front fork action in accordance with the rider’s weight and track condition.
- Harder springs stiffen the fork action and accelerate the rebound damping.
- Softer springs soften the fork action and slow down the rebound damping.
Fork Height Adjustment
- Steering is greatly affected by the fork height. The less the fork height, the lighter the front end becomes, and the greater the tendency for understeering and washout due to weight biasing. Increasing the fork height has opposite effects.
- Be sure that the front tire does not touch the fender
- when the fork is fully compressed. Make this adjustment in 10 mm steps.
NOTICE
Both fork heights should be adjusted evenly.

Standard Fork Height
Between the top end of the outer tube and the upper surface of the steering stem head.